Third-party certified cooling equipment for critical infrastructure, including hazardous environments
With over 40 years experience developing HVAC for the petroleum, power generation, and petrochemical industries, we have manufactured hundreds of systems for these applications.
We understand the need to keep critical processes running, so our all-in-one packaged severe duty HVAC units offer the most reliable environmental control available. Our explosion proof HVAC systems are designed to operate in extreme conditions from sand-filled desert heat to frozen ice caps.
To meet the specialized needs of these critical components of infrastructure, we offer pre-engineered option packages for buildings an enclosures including:
- General Purpose locations such as pipeline pumping stations
- Class I Division 2 locations such as process drive buildings in an offshore processing facility
- Class 1 Division 1 locations such as those near petroleum or natural gass offloading terminals
Key Features & Benefits for the Oil & Gas Market
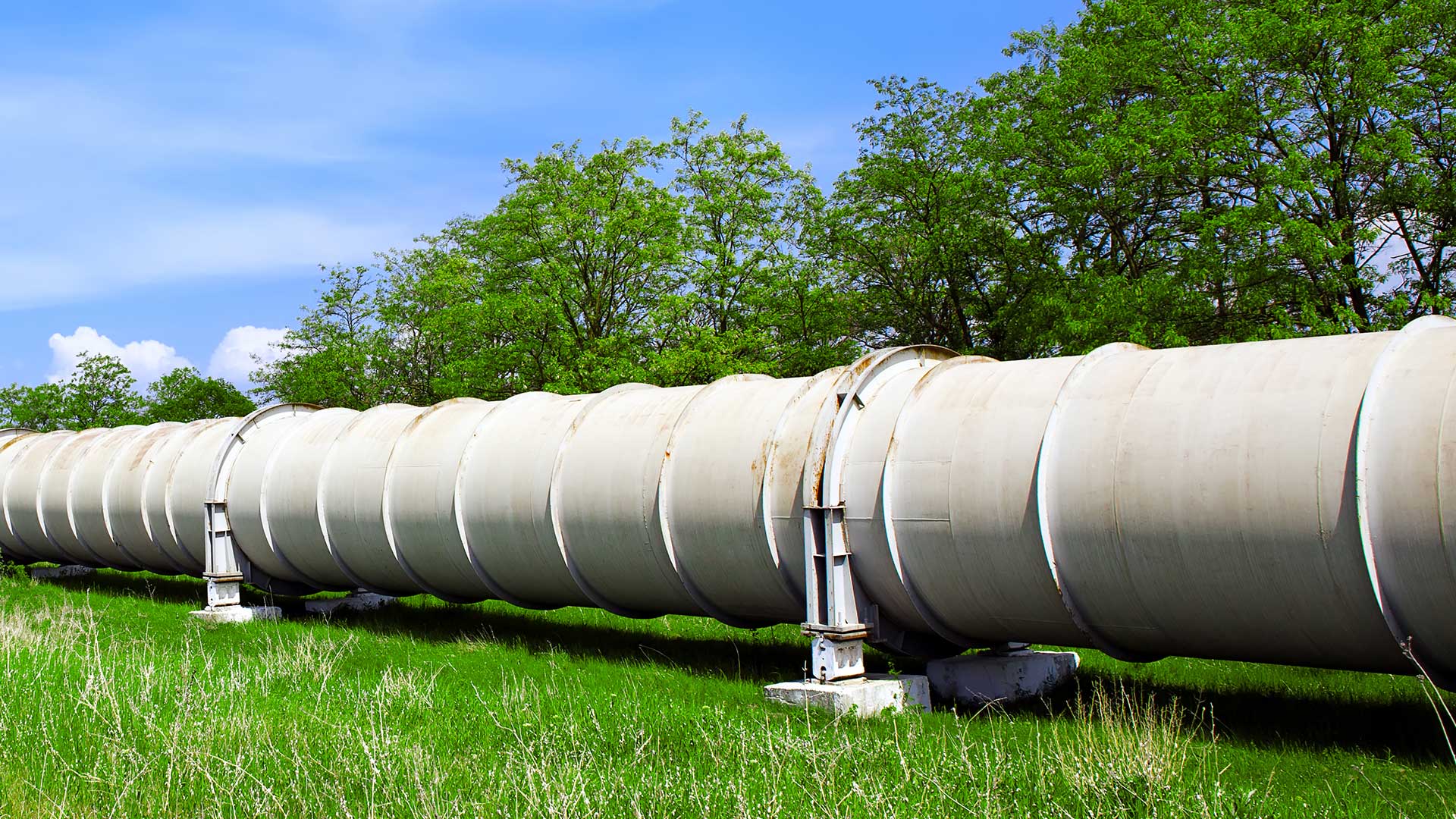
Redundancy Built-In
Downtime is costly - Specific Systems helps keep Your Business Running
- Two-stages of cooling allows for more precise cooling as well as a 50% refrigeration backup in the event of a leak or component failure
- Auxiliary fans available for additional airflow or to serve as a backup blower
- Lead lag controls reduce wear on mechanical components
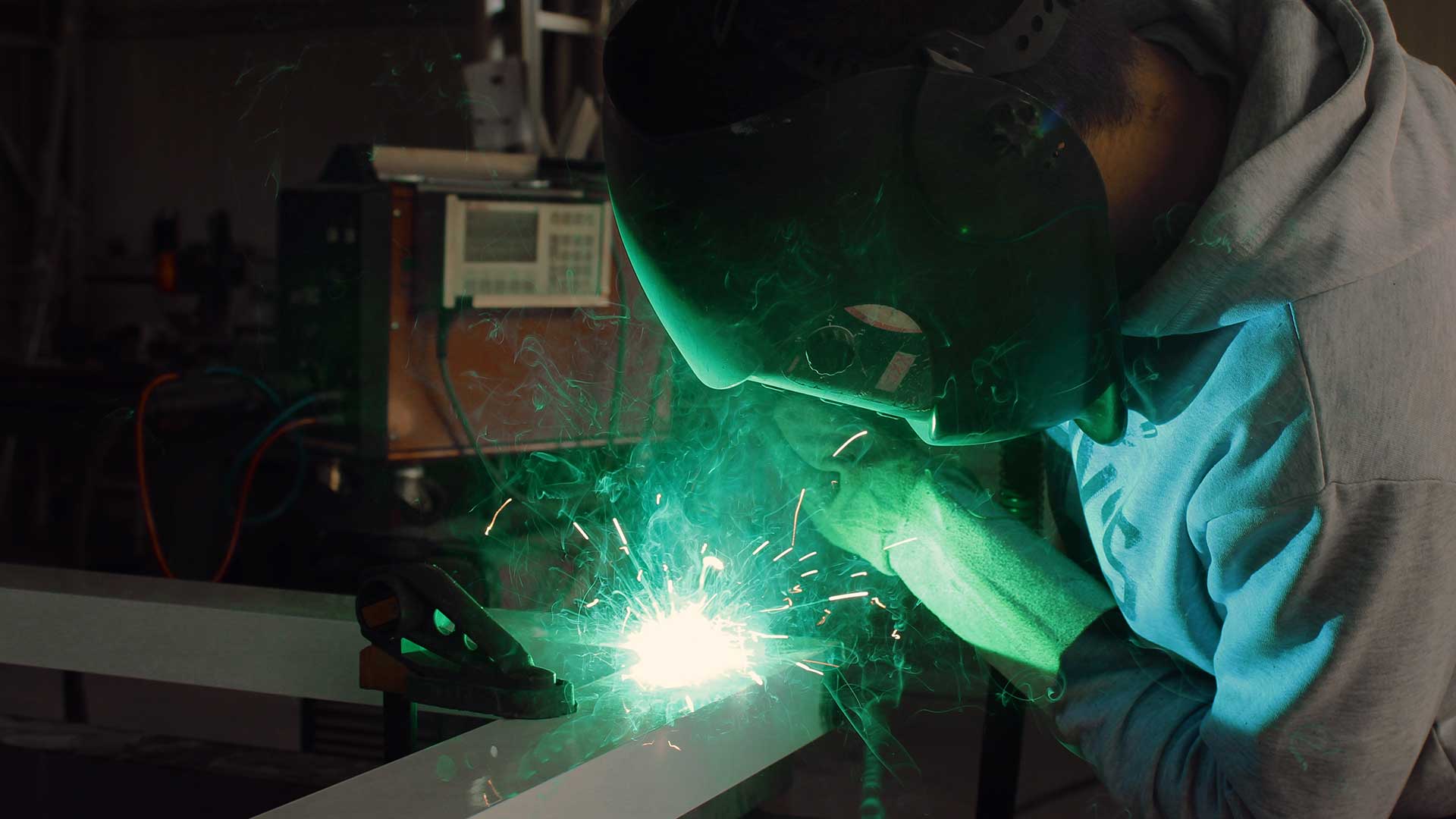
Industrial Grade
Manufactured for Long-Term Durability
In Harsh Environments
- 16-gauge powdercoated galvanized steel or 316 stainless steel cabinets
- Corrosion resistant coil coatings (SpecificCoat, Heresite, Technicoat, or Ecoat)
- Fully-coated condenser section to protect components under constant attack from the elements
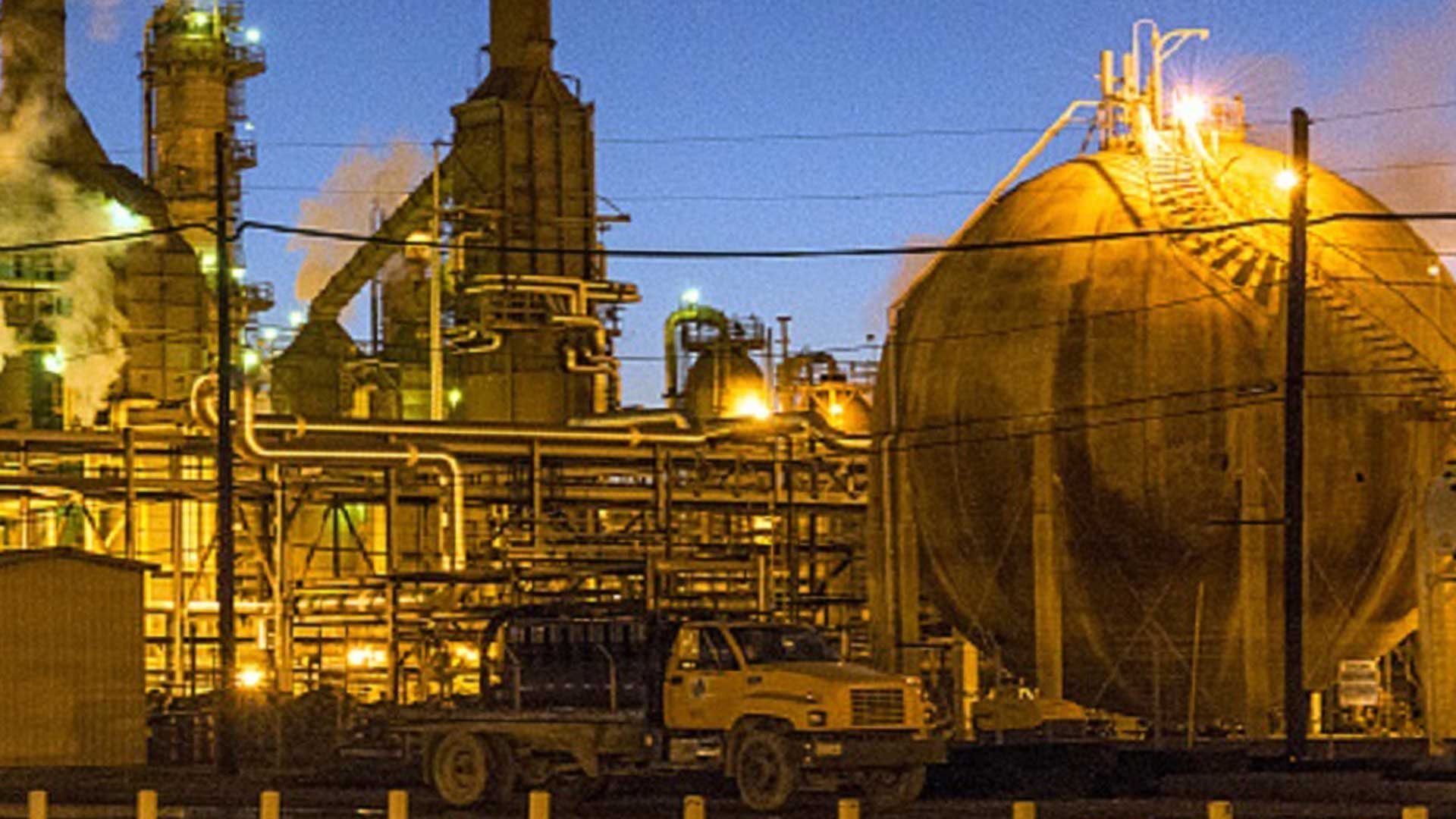
Safe, Simple Solution
Third-party Certified, Made-to-Order,
Ready for Installation Systems
- All-in-one design to allow a single point of connection
- Improved maintenance and spare parts availability
- Fully CSA certified to UL 1995 (general purpose) and 1203 (hazloc) standards
- UL 508A Listed electrical panels for safety
Providing third-party certified safe cooling to critical applications in hazardous environments
With over 40 years experience developing HVAC for the petroleum, power generation, and petrochemical industries, we have manufactured hundreds of systems for these applications.
We understand the need to keep critical processes running, so our all-in-one packaged severe duty HVAC units offer the most reliable environmental control available. Our explosion proof HVAC systems are designed to operate in extreme conditions from sand-filled desert heat to frozen ice caps.
To meet the specialized needs of these critical components of infrastructure, we offer pre-engineered option packages for buildings an enclosures including:
- Class 1 Division 1 Hazardous Locations
- Class 1 Divisioun 2 Hazardous Locations
- General Purpose
Features and Benefits
Explosion proof design
- Class 1 Div 2 labeled AMCA Type A spark-resistant TEAO evaporator motors
- Class 1 Div 2 labeled AMCA Type A spark-resistant TEFC condenser motors
- Optional built-in NFPA 496 compliant purge & pressurization
- Optional corrosive, toxic, and combustible gas alarms
- Standard or freestanding fresh air intake stack to help meet NFPA-496
Corrosion resistance
- 16-gauge galvanized steel with industrial powdercoat finish
- Optional corrosion resistant condenser coating
- Optional corrosion resistant coil coatings (SpecificCoat, Heresite, Technicoat or Ecoat)
Air Filtration
- Optional built-in chemical filtration system including MERV-8 pre-filter, two banks of chemical filtration media, MERV-8 final filter. (All filtration can be upgraded to MERV-11, MERV-14, or higher)
- Standard washable foam return air filter
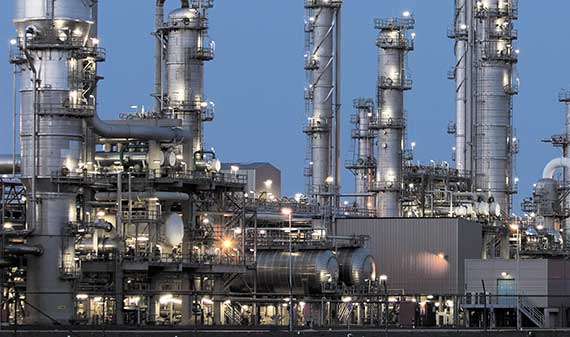
Providing cooling for high sensible load applications such as remote instrument enclosures and variable frequency drive shelters.
Despite political struggles, LNG and crude oil pipelines continue being approved by governments and constructed across thousands of miles of land worldwide. Along with the creation of jobs, both direct and indirect, the pipelines create a large demand for electricity at each of the pumping station sites in order to power the large VFDs that control the flow of material. The VFDs generate tremendous amounts of heat that must be dissipated quickly, before it causes a critical failure of the equipment.
Even worse, the pumping stations are often unmanned, and in the middle of sparsely populated areas, making access to them difficult, time consuming, and extremely costly, especially in the event of a process failure. It is for cases like this that our units are purpose built, with included 50% redundancy and time-proven, industrial grade build quality.
Recommended Options
Reverse Airflow
You know that heat rises. So when trying to remove the heat, it stands to reason that it would be easier to remove it from the top of a room. Therefore, in many cases, ducting the return air directly to an HVAC unit configured to have return at the top and supply at the bottom can provide improved circulation and help to keep the building cooler.
Since many VFDs are designed to pull cool air from down low and exhaust it into the air above, this can be even more important. If the building is on piers, another option is to hook supply air directly to the VFDs through ductwork under the building, while leaving the return air unducted.
N+1 Redundancy
Along with our inherent 50% redundancy, critical applications need full reassurance that a process will not shut down in the event of a unit failure. Including an additional complete unit on the building will further minimize the potential for downtime, as well as help improve the life of the systems themselves through a lead-lag multiplexor that automatically rotates which units are in use.
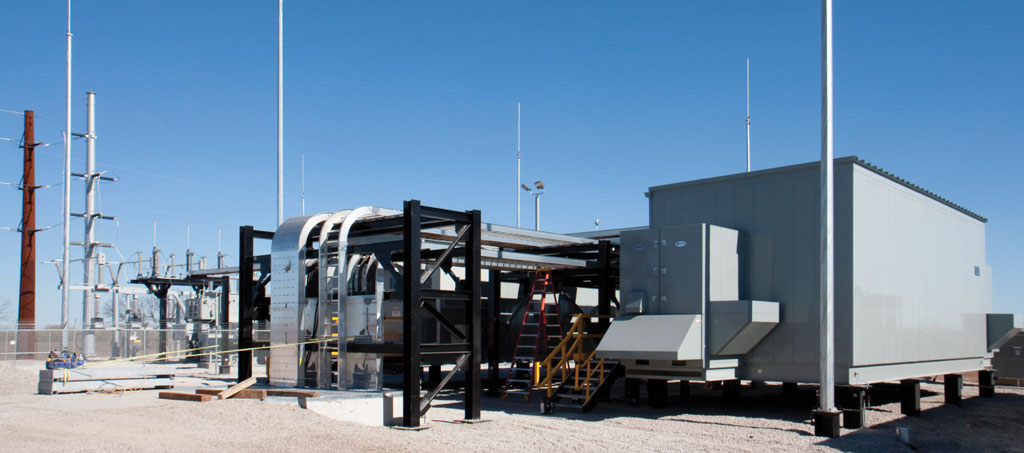
Full explosion proof redundancy for drilling platforms and critical on-site support buildings
As one of the dirtiest, noisiest, and most hazardous applications for which we provide systems, drilling rigs have a special set of needs, most importantly full redundancy. Unplanned stoppages of the drilling process can potentially cost thousands of dollars for each minute the system is down. There are several applications, unique to each part of a drilling process.
Driller’s Cabin – Recommended Options
Specific Systems has been safely providing cooling to both personnel and equipment in a Class 1 Division 1 hazardous environment for years. In fact, our InPac® 660 5-ton can be used in most instances of this application to serve as a fully redundant single unit with the inclusion of the following features:
- Space saving 42” wide cabinet
- Inherently redundant dual 2.5-ton refrigerant circuits
- Class 1 Division 1 explosion proof design
- Built-in NFPA 496 compliant purge and pressurization
- Redundant auxiliary evaporator motor and blowers
- Redundant auxiliary condenser fan
- Easy access washable filtration
- Corrosion resistant baked phenolic coil coating
VFD Building – Recommended Options
- Reverse airflow general purpose or C1D2 systems, dependent on proximity to wellhead
- Interior ducting to quickly dissipate heat loads from drives
- Corrosion resistant baked phenolic coil coating
- Additional easy access dust filtration
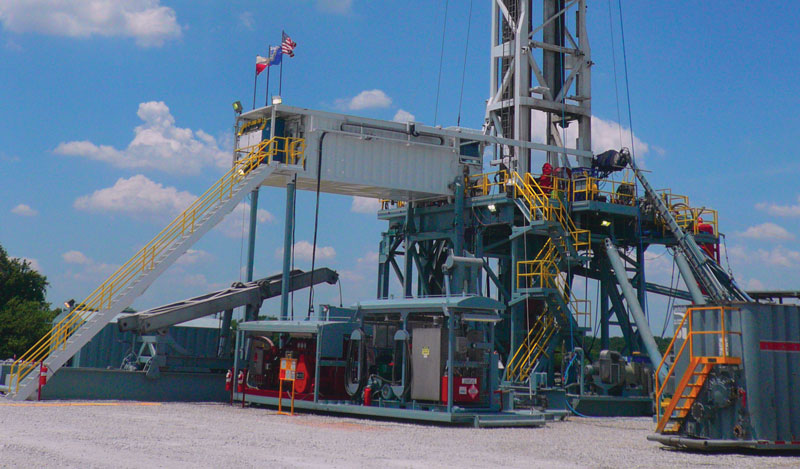
Each application brings with it unique challenges and opportunities for improvement of the status quo, and there are few environments more challenging than an offshore oil and gas platform. Take one of the most corrosive environments on the planet and add in hazardous and corrosive chemicals with tremendous space restraints and it’s no wonder few companies are able to build HVAC for these applications.
Through 40 years, we have acquired and developed thorough knowledge of the needs of offshore applications. Now, in order to better accommodate the needs of our offshore customers, we have configured a set of options to help you preconfigure your unit. Combining corrosion resistance and a minimized footprint, these options packages can be applied to our InPac® units for excellent results and long-life in offshore applications.
Recommended Options
Corrosion Resistance
- 316 stainless steel cabinet
- Copper fin/copper tube coils with Technicoat baked phenolic coating
- Fully-coated condenser section to protect components under constant attack from the elements
Explosion proof design
- Class 1 Div 2 IEEE 45 marine duty motors
- H2S and combustible gas alarms
Cabinet Configuration
With floor space at a premium on an offshore platform, where can you put a huge HVAC system? Our InPac® units offer several configuration options allowing them to adapt to each platform’s unique needs. Standard through-the-wall units are available, as well as a low profile roof-mounted option designed to minimize height requirements while maintaining capacities and airflow.
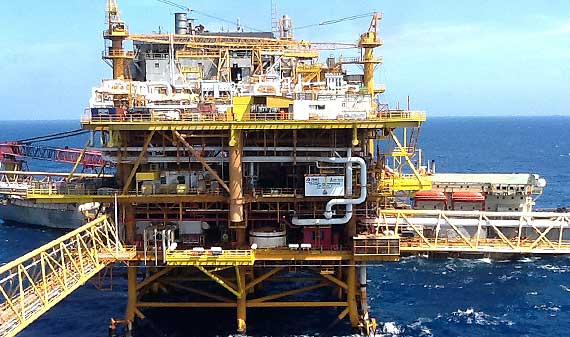